by Bill Ball
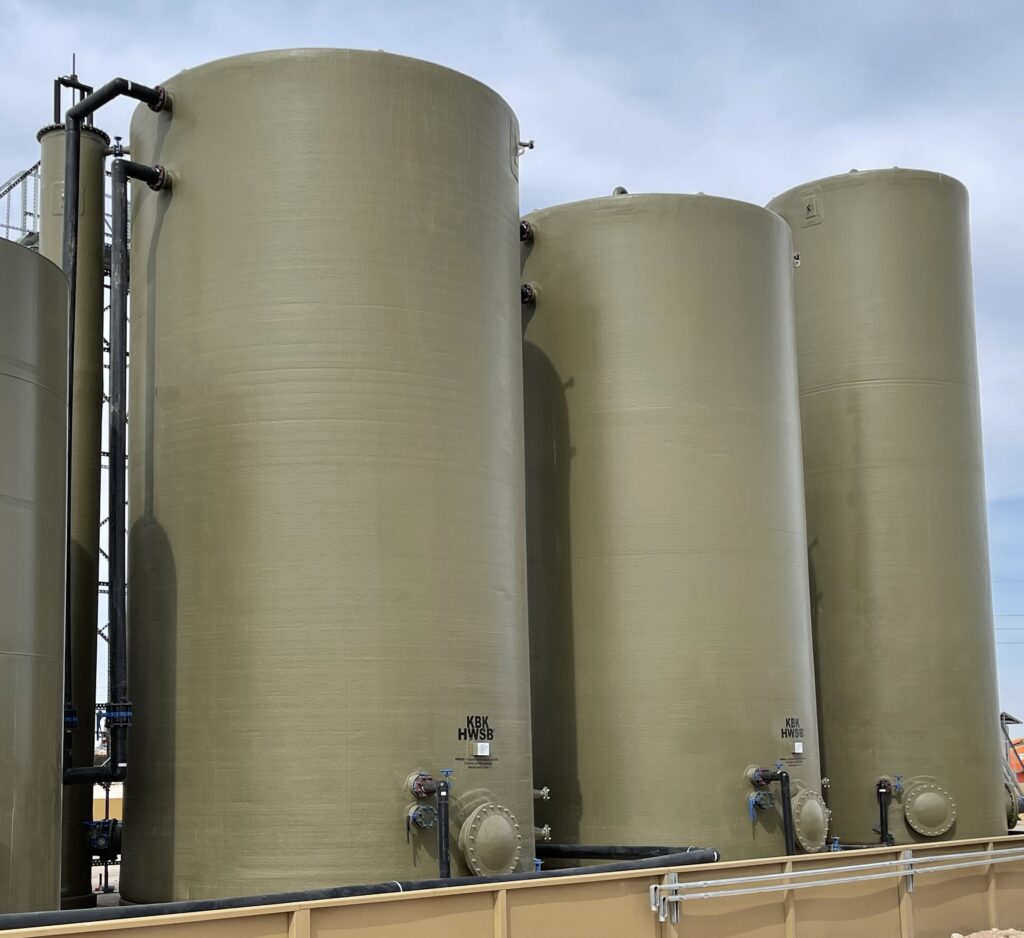
In the ever-evolving oil and gas industry, one element has remained a constant challenge—produced water management. For decades, salt water disposal (SWD) plants have played a critical role in handling the vast amounts of water generated alongside oil production. However, traditional SWD plant designs, especially those before 2008, were riddled with inefficiencies, leading to low oil capture rates, poor water quality, and frequent well plugging.
Today, advanced SWD designs are transforming the industry. Modern innovations, such as KBK’s patented HWSB® skim tank and DFSD® technology, offer revolutionary improvements in oil recovery and plant performance. These cutting-edge solutions help plant owners increase profitability, reduce operating costs, and minimize disposal well issues. Let’s explore the journey of SWD plants and how these modern innovations are changing the game.
The Early Days of SWD Plants: A Focus on Cost, Not Performance
Historically, SWD plants were designed with minimal investment in technology, often prioritizing capital expenditure (CAPEX) savings over long-term performance. In the late 1800s, gunbarrel tanks were the standard for oil-water separation. While suitable for small water volumes, gunbarrel tanks struggled as water production surged with increased oil output, leading to low oil recovery and rapid well plugging.
By 1992, the limitations of traditional systems became glaringly evident. The inefficiencies in oil separation meant that much of the oil—along with solids—was sent into disposal wells, leading to frequent and expensive workovers. As environmental regulations tightened, it became clear that a more efficient solution was needed.
Enter KBK’s HWSB® and DFSD® Technologies: A Game Changer
In response to these challenges, KBK Industries developed the HWSB® skim tank and DFSD® technology, both of which revolutionized SWD plant designs. The HWSB® skim tank optimizes oil separation, capturing over 99.99% of the oil, while the DFSD® focuses on removing solids from the water before it reaches the skim tank. Together, these technologies dramatically improve plant performance and oil recovery rates.
With HWSB® technology, SWD plants now recover significant quantities of oil that would have otherwise been lost. For example, a 15,000 BWPD (barrels of water per day) plant with a single HWSB® can recover over 100 barrels of oil per day, adding substantial revenue to the plant’s bottom line. This additional oil revenue pays for the technology upgrades in a matter of months.
Benefits of Modern SWD Designs
The impact of modern SWD designs goes beyond just oil recovery. Here are some key benefits:
- Reduced Disposal Well Plugging: By removing more oil and solids from the water before injection, modern SWD plants experience fewer disposal well issues. This reduces the need for costly workovers, saving operators between $150,000 and $1 million per workover.
- Lower Operating Costs: By minimizing water storage and optimizing tank design, modern plants cut down on the risks of bacterial growth and contamination, lowering overall OPEX.
- Improved Water Quality: Efficient separation technologies ensure that water injected into disposal wells meets higher quality standards, preserving injectivity and extending the life of the well.
- Higher ROI: With more oil recovered for sale, plants see a faster return on investment. In fact, the cost of upgrading to modern technology, such as the HWSB® skim tank, can be recouped in just one month of operation.
Conclusion: Why It’s Time to Upgrade Your SWD Plant
If your SWD plant is still using outdated gunbarrel tanks or lacks modern automation, it’s time to consider an upgrade. The HWSB® skim tank and DFSD® technologies provide a cost-effective solution to maximize oil recovery, reduce operating expenses, and enhance disposal well performance.
The future of salt water disposal is here, and the benefits are too significant to ignore. By embracing modern plant designs, you can ensure your SWD facility remains profitable, efficient, and sustainable for years to come.
To learn more about how the HWSB® skim tank and DFSD® technologies can enhance your plant’s efficiency, contact KBK Industries today.
Read the technical paper, SWD Plant Design & Performance, …Then and Now
Bill Ball is a senior staff consultant to KBK Industries with over 50 years of oilfield engineering experience and holder of twenty-three oil and gas industry related US patents. His credentials represent the culmination of a lifetime of breakthroughs and innovations. Bill’s twenty-three US process equipment patents speak to this. His first patent has become an industry “game changer.” It is the industry’s first true oil-water separation “skim tank”, the “HWSB”. Today there are over 3,500 HWSB® skim tanks separating and capturing oil that used to be injected and lost forever. Bill resides in Bixby, a suburb of Tulsa, Oklahoma.