Limitations & Disadvantages of Fiberglass Tanks
Fiberglass tanks are popular in various industries, including oil and gas, due to their corrosion resistance and lightweight properties. However, despite their advantages, there are several disadvantages associated with fiberglass tanks that can impact their performance and suitability depending on the application
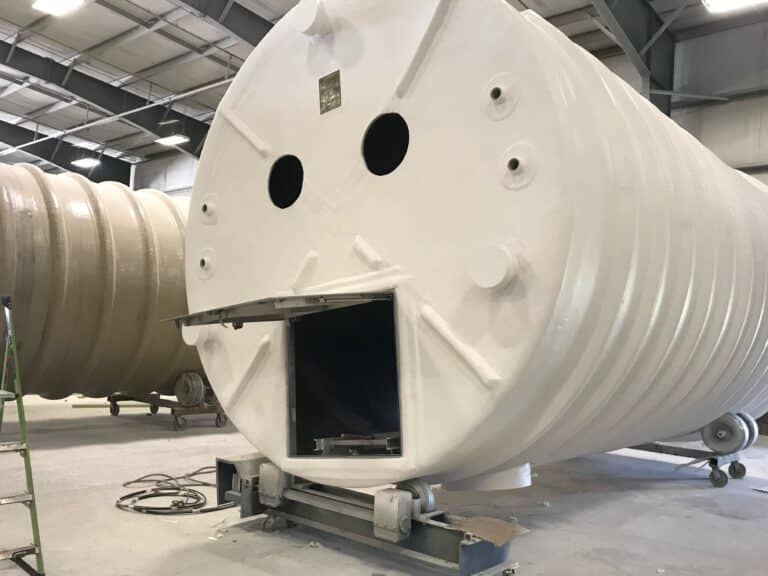
What are the disadvantages?
Structural Integrity Concerns
Brittleness: Fiberglass is less ductile compared to metals. It can become brittle and crack under impact or in fluctuating temperature conditions, leading to leaks or structural failures.
Low Modulus of Elasticity: The flexibility of fiberglass can be a disadvantage under certain load conditions, as the material may deform or bulge, especially in underground applications where soil pressure is significant.
Resolution: To resolve the brittleness and elasticity issues, KBK uses engineered resins which have a high modulus of elasticity. The resins KBK uses also do not become brittle like other resins do. This allows KBK’s tanks to be more resilient during shipping and that the tank will have a longer life.
Chemical Sensitivity
Compatibility Issues: Fiberglass tanks must be carefully manufactured with resins that are compatible with the stored substance. Incorrect resin selection can lead to chemical degradation of the tank.
Permeability: Some types of resins used in fiberglass tanks are permeable to certain chemicals and gases, which can lead to contamination of the stored fluid or a weakened structure due to the chemical interaction.
Resolution: KBK confirms the product to be stored and its concentration and selects the resin which offers the most corrosion resistance for the product stored. Additionally, KBK installs corrosion veils in layers for additional chemical resistance.
Temperature Limitations
Heat Sensitivity: Fiberglass tanks generally have lower thermal resistance compared to metal tanks. High temperatures can cause the resin to weaken or deform.
Thermal Expansion: Fiberglass has different thermal expansion coefficients which can cause issues with fittings and connections, potentially leading to leaks.
Resolution: KBK fiberglass tanks can be rated up to 200-degree Fahrenheit. KBK’s engineered Isophthalic resin is rated for 160 degrees Fahrenheit. KBK’s vinyl ester resin is rated for 180 degrees Fahrenheit.
Manufacturing Flaws
Inconsistencies: The strength and quality of fiberglass tanks can vary depending on the manufacturer and the manufacturing process. Poorly made tanks may have inconsistent thickness and weak spots.
Quality Control: Due to the nature of their construction, detecting flaws inside fiberglass tanks (such as air pockets or incomplete resin curing) can be difficult without sophisticated testing methods.
Resolution: With nearly 50 years of fiberglass tank manufacturing experience, KBK is the trusted leader in fiberglass tank manufacturing.
Durability and Longevity Issues
UV Degradation: Continuous exposure to sunlight can degrade the resin used in fiberglass tanks, leading to embrittlement and reduced life expectancy.
Wear and Tear: While fiberglass is resistant to corrosion, it is susceptible to wear and tear from abrasive contents or external conditions, which can gradually erode the tank’s interior or exterior.
Resolution: KBK’s tanks last 20 to 40 years with proper maintenance.
Installation and Repair Complications
Handling Sensitivity: Fiberglass tanks are lightweight, which while an advantage, also makes them susceptible to damage during handling and installation if not done correctly.
Repair Limitations: Repairing fiberglass tanks can be complex and expensive. It often requires specialized knowledge and materials to ensure the integrity of the tank is maintained.
Resolution: KBK has developed installation guides and offers field repair services that make handling and repair concerns go away.
Cost Factors
Initial Investment: While generally cost-effective in the long term due to low maintenance needs, the initial cost of fiberglass tanks can be higher than other materials, particularly if custom sizes or shapes are required.
Lifecycle Costs: The potential for damage from impacts, UV exposure, and chemical interactions can add to the total lifecycle cost of owning and maintaining fiberglass tanks.
Resolution: Because of our size and buying power, KBK offers new fiberglass tanks at the most competitive prices, making them a better choice from a price.
Environmental Impact
Fragility in Seismic Activities: In areas prone to earthquakes, fiberglass tanks can be more vulnerable to damage due to their relatively lower shock resistance compared to more elastic materials like steel.
Resolution: KBK engineers tank used in areas of wind, seismic and snow load conditions. The KBK engineered tanks perform well in these zones.
Regulatory and Compliance Issues
Standards Compliance: Meeting the stringent standards for storage tanks (such as UL, ASTM, or API specifications) can be challenging with fiberglass, especially with the wide range of chemicals and conditions they are subject to.
Resolution:
KBK is certified under API 12P and UL 1316. The American Petroleum Institute and Underwriters Laboratories certifications signify that KBK is in the elite few when it comes to certifications and standards compliance,
KBK understands the disadvantages of tanks made by some manufacturers. KBK has implemented solutions to make fiberglass tanks a leading choice for storage solutions. Custom engineered resins, industry certifications, and cost control make KBK Industries the choice when customers require a long-lasting fiberglass tank.