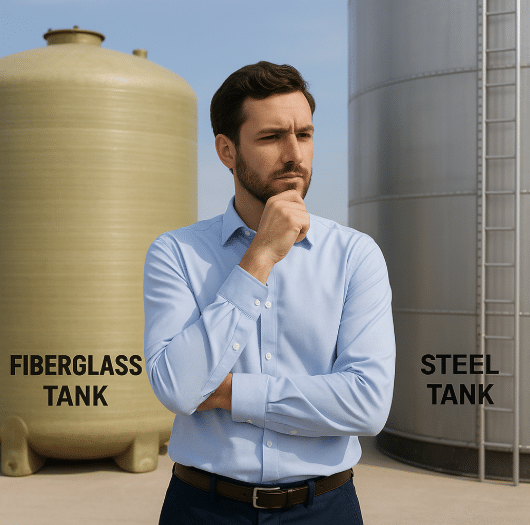
Choosing the wrong chemical storage tank can result in safety risks, equipment failure, and costly downtime. Whether your operation calls for fiberglass, steel, or a combination of both, understanding the most common mistakes helps you make a smarter, safer decision. Here’s what to avoid—and how KBK Industries helps you choose the right solution for your application.
1. Choosing the Wrong Material for the Chemical and Environment
Not all tanks are created equal. Certain chemicals corrode metal, while others may degrade plastic or composite materials over time.
– Fiberglass tanks, especially when built with vinyl ester resins, excel in storing corrosive chemicals like acids, chlorine compounds, and solvents.
– Steel tanks, on the other hand, offer unmatched strength and are ideal for high-pressure systems, flammable liquids, and applications that require grounding for static discharge.
*Pro tip: Start with a full chemical compatibility and safety assessment—KBK can help you match the tank material to your exact chemical profile.
2. Ignoring Temperature and Pressure Requirements
High heat, cold environments, or fluctuating conditions can compromise tank integrity if the wrong material is selected.
– Fiberglass tanks can be engineered with resin systems and insulation to handle wide temperature ranges.
– Steel tanks naturally withstand high pressures and are often preferred in systems with temperature extremes, rapid heating, or cooling cycles.
KBK offers tanks engineered for thermal stability and pressure demands—across both fiberglass and steel lines.
3. Overlooking Regulatory and Containment Requirements
Secondary containment isn’t just best practice—it’s often a legal requirement.
– We offer double-wall fiberglass tanks and custom-built containment basins to simplify EPA compliance.
– Steel tanks can be outfitted with skid-mounted containment trays or installed within concrete berms as part of site-specific safety plans.
Ignoring containment can lead to serious environmental damage, fines, and delays. We make it easy to stay ahead of regulations.
4. Skimping on Venting, Fittings, and Access
Off-the-shelf tanks might not offer the configuration you need for safe handling, flow control, or maintenance.
– KBK tanks—both steel and fiberglass—can be designed with custom flanged nozzles, overflow fittings, access ports, ladders, vents, and more, tailored to your process.
– Fiberglass tanks offer greater flexibility for embedding specialty fittings during fabrication, while steel may offer faster modifications in the field.
Avoiding this mistake upfront saves costly retrofits and operational headaches later.
5. Failing to Plan for Growth or Site Constraints
Your tank system should grow with your business.
– Fiberglass tanks are lightweight and modular, making them easier to expand, relocate, or repurpose down the road.
– Steel tanks may be more suitable for long-term, permanent installations or when additional structural support is needed.
Whether you’re dealing with tight site footprints, future expansion, or permits, KBK helps you plan ahead with scalable solutions.
A Smarter Storage Strategy, Built for You
At KBK Industries, we don’t just build tanks—we build long-term solutions. Our team works with you to identify your exact needs, from chemical compatibility to future scalability, and recommends the best material and design for your operation.
Avoid these costly mistakes—partner with KBK for custom-engineered tanks that last.
📞 Contact us today for a consultation or explore our fiberglass and steel tank options.